Case study
How Frexco creates
the next generation warehouse operation
Frexco waved away periodic Excel number crunching and printed lists to manage warehouse operations in Jestor, bringing real-time efficiency through internal apps and a completely remote experience to the field team.
500+
Restaurants
USD 100,000+
MRR
About Frexco
Frexco connects small and medium farmers directly to urban consumers (both businesses and individuals) to create the best fresh produce supply chain solution in Brazil.
Physical tasks shouldn’t mean everything is offline
Frexco is a startup that has to run like clockwork. When dealing with perishable products, there’s little room for error: buy too much of a product and you end up throwing it away, but not buying enough makes you run out of stock (and leaves a sour taste in the customer’s mouth).
And, of course, even perfect business intelligence can only do so much with outdated data. If something spoils or if a shipment is returned, you need that information right away.
In that regard, Frexco found itself with a problem most companies with field operations face: no software that efficiently connects field to office to provide real-time information.
Frexco’s warehouse was running on a combination of printed lists, texts and end of day counting. It wasn’t impossible to handle yet, but an expanding portfolio and growing sales meant things could start to break soon.
That’s when Frexco’s team turned to Jestor to bring their warehouse to the next level by:
1. Having real-time data, all the time;
2. Automating tasks and purchases;
3. Always knowing what happened, and why.

”Jestor brought a new level of efficiency to our operation. By automating purchases and giving data autonomy to every team member, we now have true real-time data. The warehouse is now as tech-driven as the office, and time that would be spent dealing with spreadsheets is now used for planning and improving our core business.”
Eduardo Pietraroia
Co-Founder at Frexco
Automating complex processes to enable growth
Frexco understood that the only true way to scale field operations is automating data exchange. If new orders are placed, the field team has to know immediately. If a shipment is partially unusable, the office must react accordingly.
Thankfully, Jestor’s smartphone-friendliness provided Frexco with the perfect way to build internal apps and databases that did just that: team members in the field could send and receive information on-the-go.
Before Daily Excel spreadsheets manual update Every day, a new Excel file would be created and fed with start-of-the-day stock numbers, clients’ orders placed and sales projections. This would result in a list of products to buy, and the team would place these orders by manually sending WhatsApp messages to the suppliers. | After Automatic purchase forcasting Jestor always has up-to-date stock numbers and suppliers’ delivery estimates. The platform receives the clients’ orders and sales projections to generate a daily list of produce to buy, sorted by suppliers. Jestor also generates an automatic WhatsApp message for each supplier, saving the team precious time when placing orders. Those orders can also be marked as “Placed” to create a stock estimate, and “Received” to update stock numbers. |
Data input using a computer in a base Warehouse team had to update the spreadsheet in periodic updates, as a separate but necessary part of the process. This update was time consuming and often inefficient, as it mainly served to digitize on-site information that was collected manually. | Collecting data anywhere through the phone Each warehouse team member has a filtered access to Jestor, allowing them to see stock data and quickly perform actions that update a product’s quantity through their smartphone, effectively allowing them to upload real-time data as they carry on their routine. This decentralized approach makes it so there’s no need to crunch numbers by the end of the day. |
Print out lists Frexco’s team printed out lists with the expected product quantities to separate for delivery, and then continuously checked for new orders and compared the numbers to see if they underestimated demand. | Real time lists Jestor automatically generates a list of product quantities to separate, and updates this list whenever demand exceeds the initial expectation. This means the team members only need a quick glance at their Jestor to see if they need to separate more of a product. |
”Jestor brought efficiency to just about every step of the process. Not having to manually type orders is a godsend, and being able to do everything through a smartphone makes sure things only need to be done once. It’s easy too: some processes are as simple as marking a checkbox.”
João Marcos Jesus
Quality and Planning Analyst
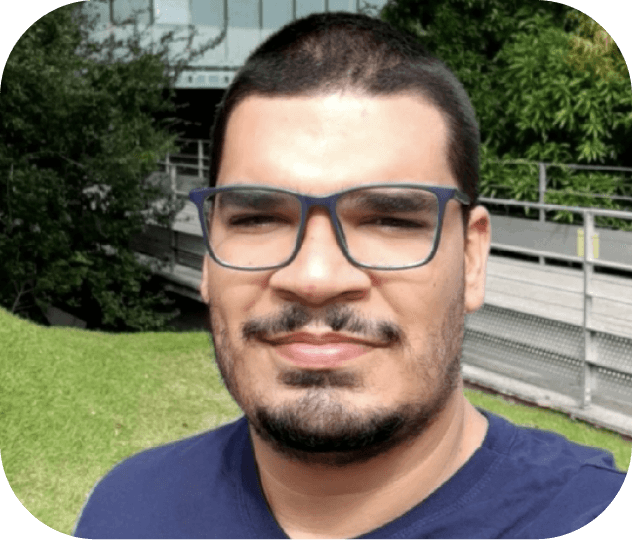
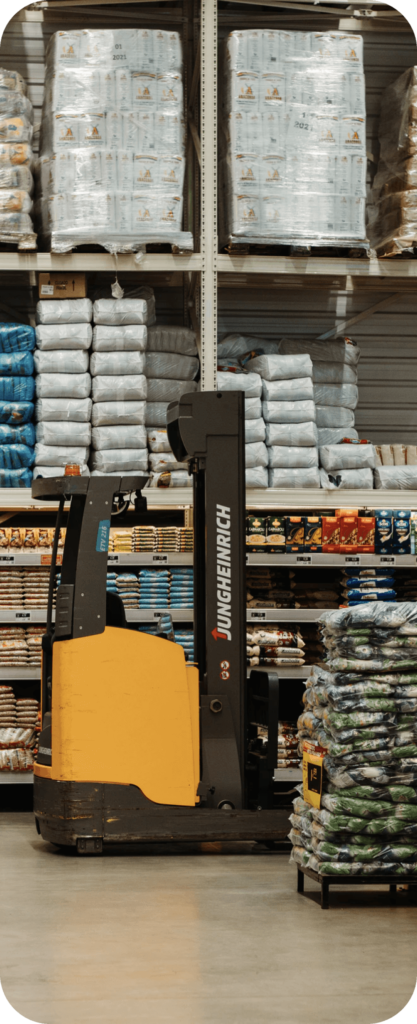
Automations and data
structures are a must for
growth
Frexco not only made their current process more efficient, but they laid out the groundwork to allow for growth without chaos. Each automated process ensures that the effort to handle 100s or 1,000s products remains largely the same. Also, operations with real-time updates prevent stressful, long number crunching night sessions from becoming the norm.
Jestor’s data structure and freedom to code their own solutions also allow them to iteratively expand the platform’s capability to become more and more integrated. Jestor is swiftly expanding to encompass other parts of the operation, such as updating the ecommerce platform numbers and taking data automatically from other previously implemented databases.
This means Frexco can have a solution that is increasingly tailored to their needs without having to worry about developing back office technology. They can keep focusing on the core of their company: finding better ways to connect households and businesses with small farmers, all while refining their ability to predict demand and reduce the waste from traditional fresh produce supply chains.
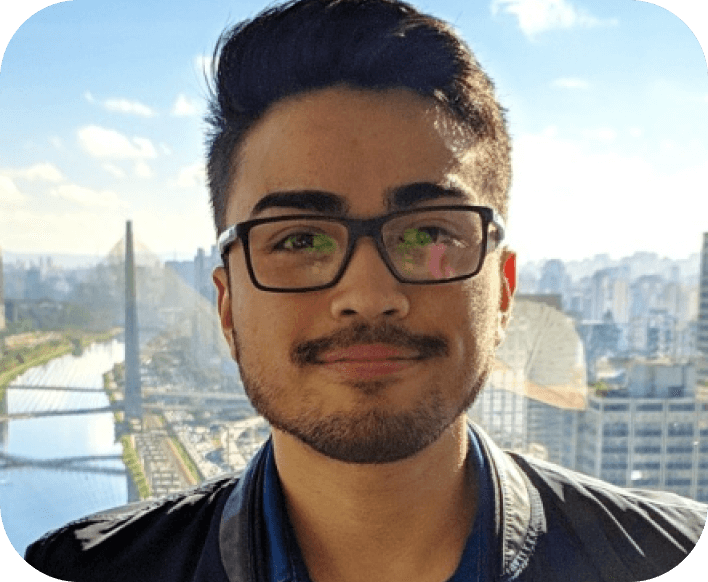
”Jestor allows development teams to build fast and focused. Everything is accessible through the API, and internal lowcode automations let processes be as unique and complex as they need to be. In Jestor a single developer can deliver an internal app with the efficiency of a whole team, and non-tech teams can be part of the process too.”
Vinícius Issamoto
IT Specialist
A company wide platform
While Jestor was brought in to solve a complex stock management problem, it’s expanding to help Frexco with a lot of other internal processes. That’s because Jestor’s flexibility ensures it can tackle any sort of problem, and the platform is structured to be used company-wide, not to be a single team island.
For example, a separate inventory system for internal items (such as office supplies) was created, bringing to the table a request and approval process that ensures everything is accounted for, as well as saving a history of purchases and prices.
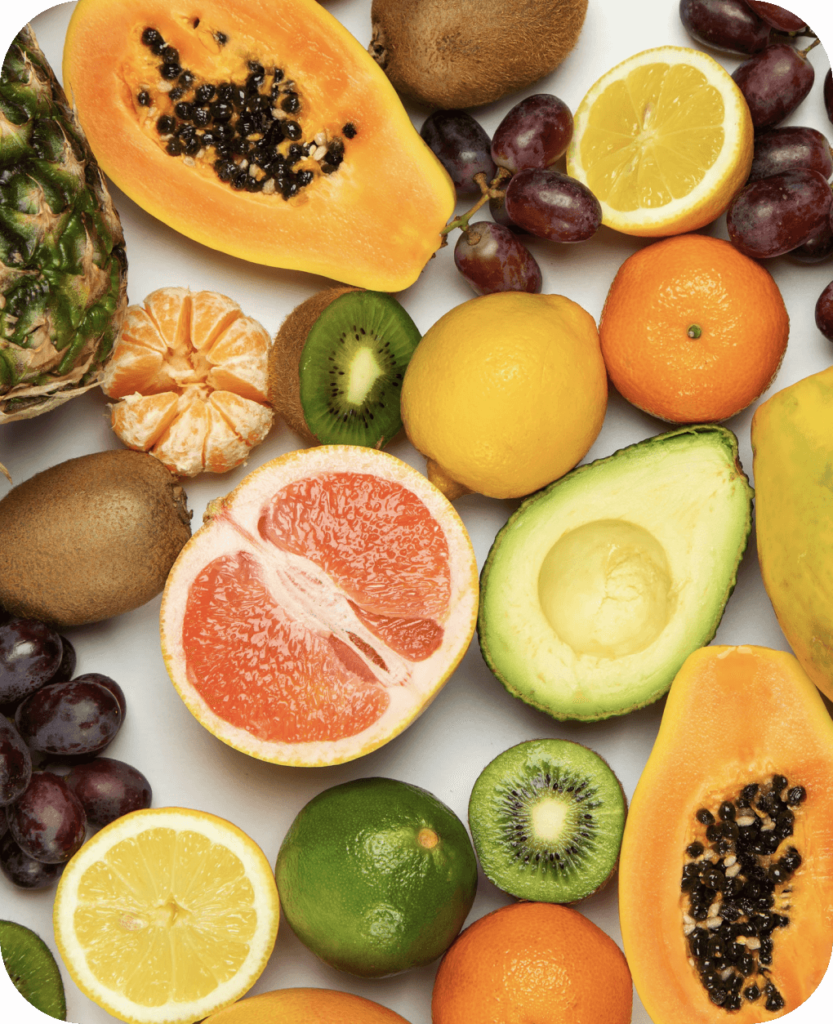
“Processes that were put together with an assortment of different software are now all inside in Jestor. Not only this streamlines our daily routines, but having data in one place is a must for organization. It’s hard to check on previous history when data is spread between emails, text messages, spreadsheets and different workflow platforms.”
Andressa Moreno Sugae
Procurement Manager at Frexco
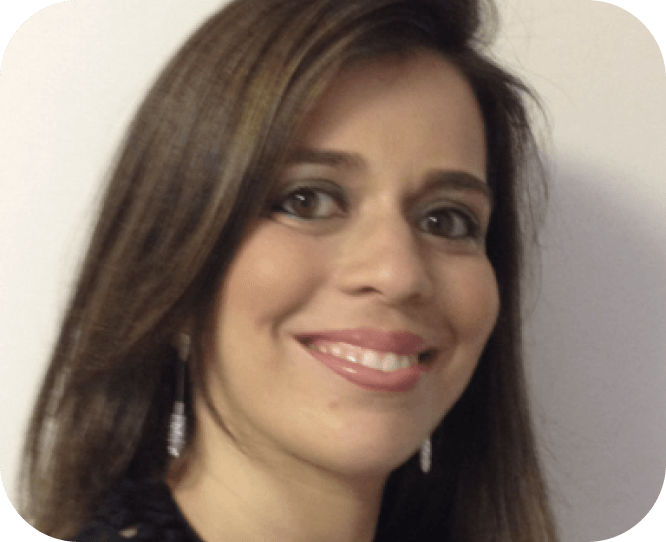